The Value of Utilizing a Chemical Defoamer in Numerous Applications
The application of chemical defoamers is a crucial factor to consider throughout several industries, consisting of food processing, wastewater treatment, and pharmaceuticals. These representatives play a critical role in mitigating foam development, which can impede performance and compromise product high quality. The benefits of using defoamers expand beyond plain looks; they are critical for attaining compliance with market requirements and improving operational processes. The mechanisms by which defoamers operate and their details applications elevate further concerns concerning their general impact and performance in these varied contexts. What understandings can be uncovered about their use?
Comprehending Foam Formation
Foam development is a complicated physical sensation that takes place when gas bubbles are trapped within a liquid matrix, resulting in the development of a stable framework. This process can be affected by different variables, consisting of the thickness of the liquid, the surface area tension at the gas-liquid interface, and the visibility of surfactants. Surfactants lower the surface area stress, advertising bubble production and stablizing, which typically results in the formation of foam in many industrial procedures.
Foams are commonly encountered in applications such as food production, wastewater therapy, and chemical manufacturing. In these contexts, foam can act as an insulator, disrupt mixing procedures, or impede the effectiveness of equipment. The security of foam is figured out by the balance between the forces acting to maintain the bubbles and those that advertise their collapse.
Comprehending the mechanics of foam formation is crucial for successfully handling its existence in different systems. By understanding the underlying principles, industries can devise techniques to alleviate unwanted lathering, consequently improving functional efficiency and product high quality. This fundamental knowledge offers as a forerunner to exploring the utility of chemical defoamers, which specifically deal with foam-related obstacles in many applications.
Advantages of Chemical Defoamers
Chemical defoamers provide substantial advantages across various markets by efficiently lowering and controlling foam formation. By lessening foam, chemical defoamers assist keep optimum manufacturing prices and decrease downtime linked with foam management.
Furthermore, chemical defoamers add to boosted product top quality. Lathering often leads to inconsistencies in formulations, which can negatively impact the final item. By managing foam levels, defoamers make certain harmony, consequently enhancing the total top quality of the result.
Cost-effectiveness is another noteworthy benefit (Chemical Defoamer). By reducing the quantity of basic materials needed for production and reducing waste, chemical defoamers can cause substantial savings. Moreover, they often enable reduced energy usage, as processes can run a lot more efficiently and call for much less intervention.
Applications in Food Processing
In the food processing sector, efficient management of foam is vital to ensure both item quality and operational effectiveness. Foam can disrupt different procedures, from blending and mixing to product packaging, causing reduced yields and prospective contamination. Chemical defoamers play an important duty in minimizing these concerns by quickly damaging down foam, allowing for smoother operations and improved item consistency.
In applications such as milk processing, defoamers prevent excess foam formation throughout the production of cheese, yogurt, and milk, which can disrupt equipment and impact the structure of the end product. In developing and fermentation procedures, foam control is crucial to preserve the integrity of the beverage and ensure optimal fermentation rates.
In addition, chemical defoamers are utilized in food solutions, sauces, and dressings to boost the stability and appearance of the end products. By lessening foam throughout production, producers can accomplish much better mixing and dispersion of components, leading to exceptional top quality. Overall, the incorporation of chemical defoamers in food processing is essential for preserving effectiveness, high quality, and safety and security in food manufacturing.
Duty in Wastewater Treatment
Reliable foam monitoring is equally vital in wastewater treatment processes, where extreme foam can hinder operations and make complex the therapy of effluents. In numerous wastewater therapy facilities, foam can form as a result of organic task, surfactants, or various other natural products existing in the influent. This foam can result in a variety of operational challenges, including decreased treatment effectiveness, raised maintenance requirements, and prospective regulative conformity concerns.
Chemical defoamers play a critical duty in reducing these difficulties. By decreasing the surface area tension of the fluid, defoamers promote the collapse of foam frameworks, thus assisting in smoother procedure of devices such as aeration tanks and clarifiers. Their timely application helps maintain optimum hydraulic problems, enhancing the general performance of solids splitting up processes.
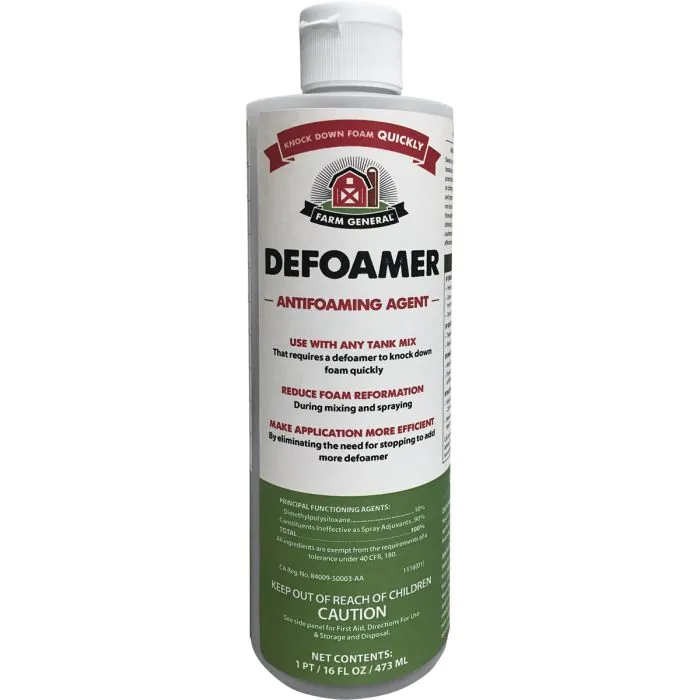
Impact on Pharmaceutical Production
Foam control is essential in pharmaceutical production, where the presence of excessive foam can disrupt manufacturing procedures and concession item high quality (Chemical Defoamer). The formation of foam throughout various phases, such as mixing, blending, and fermentation, can bring about ineffective mixing, insufficient warm transfer, and even devices damages. These issues not just cause operational hold-ups but can additionally trigger substantial financial losses and impact conformity with strict governing requirements
Chemical defoamers are particularly created to reduce these difficulties. By properly minimizing foam formation, they improve procedure performance and preserve the stability of the final product. In specific, defoamers ensure regular dosage forms, boost the stability of solutions and suspensions, and improve cleaning procedures by stopping foam build-up in tools.
In addition, using defoamers can maximize the yield of energetic pharmaceutical active ingredients (APIs) by advertising better extraction and filtration procedures. As pharmaceutical companies strive to boost product high quality while minimizing production expenses, the duty of chemical defoamers becomes increasingly vital - Chemical Defoamer. Their unification right into manufacturing protocols not just sustains compliance with Excellent Manufacturing Practices (GMP) but likewise fosters innovation and competition in a quickly developing industry
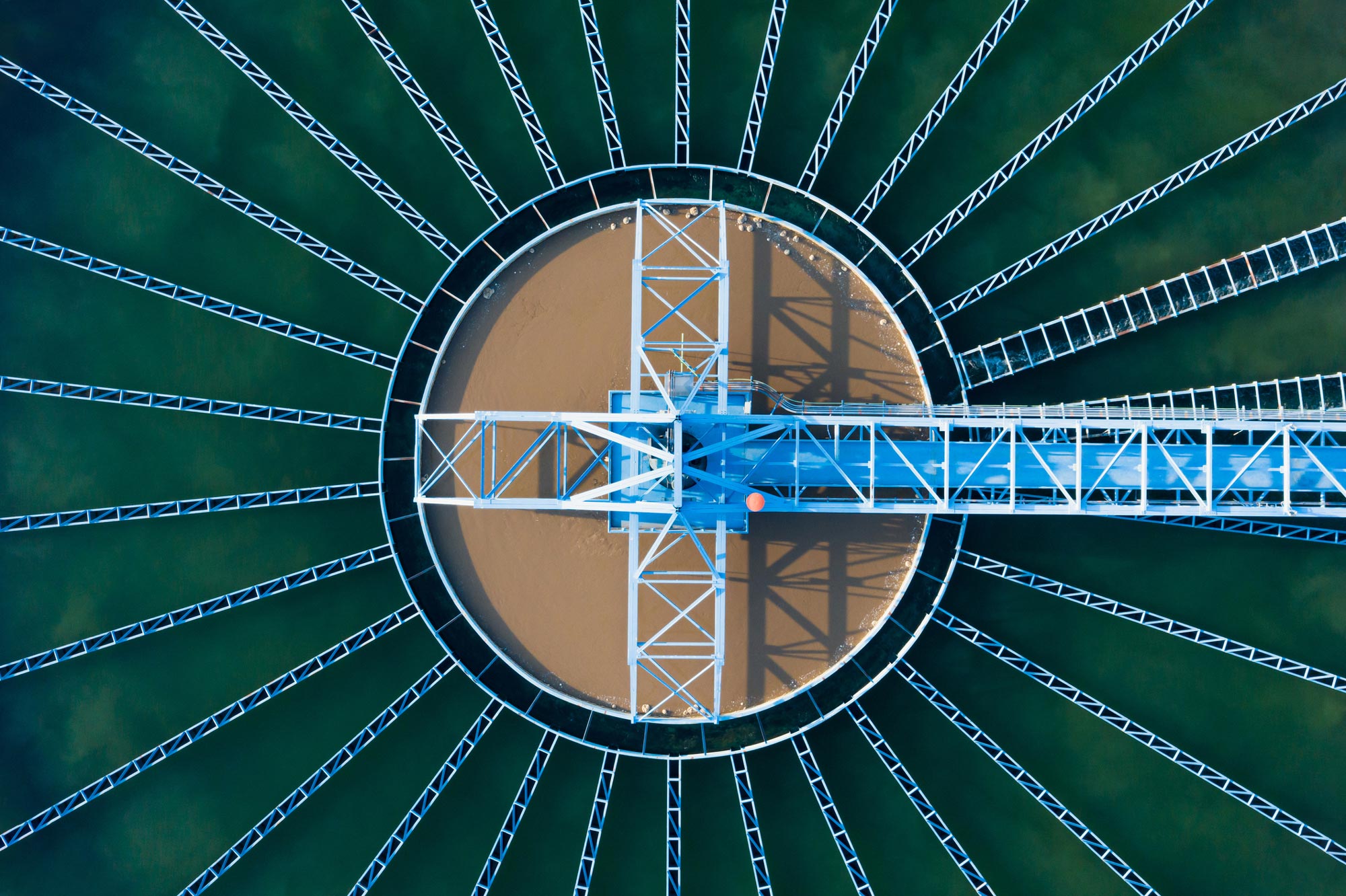
Verdict
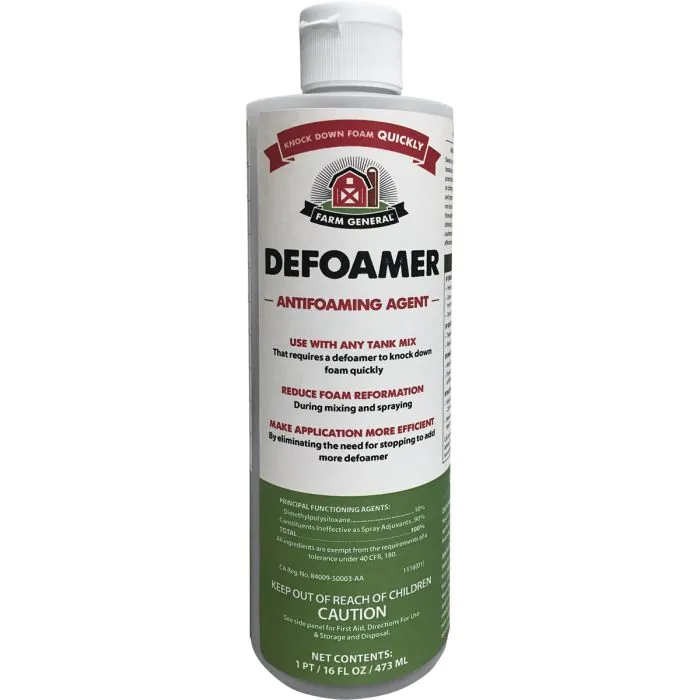
Chemical defoamers provide considerable advantages across numerous sectors by efficiently regulating and reducing foam development. By minimizing foam, chemical defoamers aid keep optimal manufacturing rates and minimize downtime connected with foam management. Chemical defoamers play an essential function in reducing these problems by swiftly damaging down foam, allowing for smoother procedures and improved item consistency.
Efficient foam monitoring is similarly important in wastewater treatment processes, where useful site extreme foam can hinder procedures and make complex the therapy of effluents.Foam control is critical in pharmaceutical manufacturing, where the visibility of extreme foam can disrupt producing processes and compromise item quality.